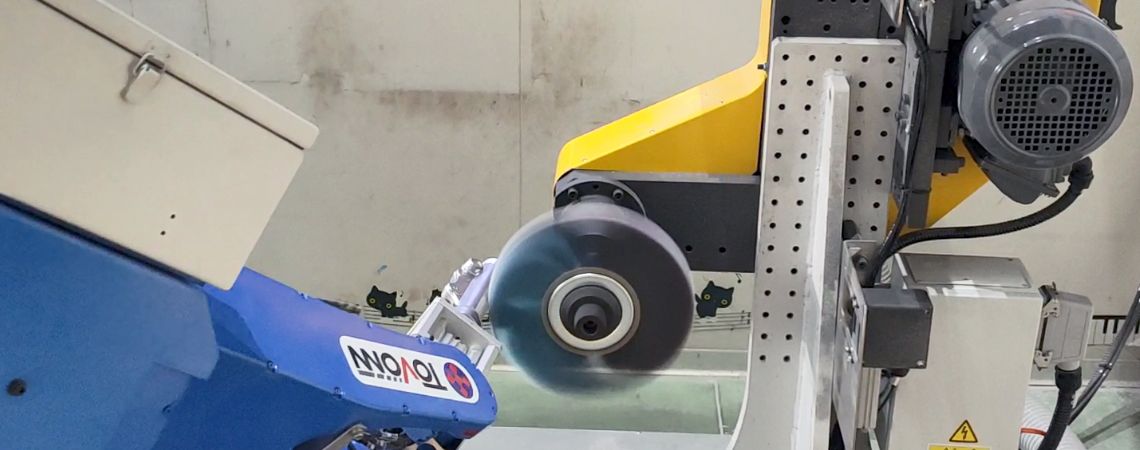
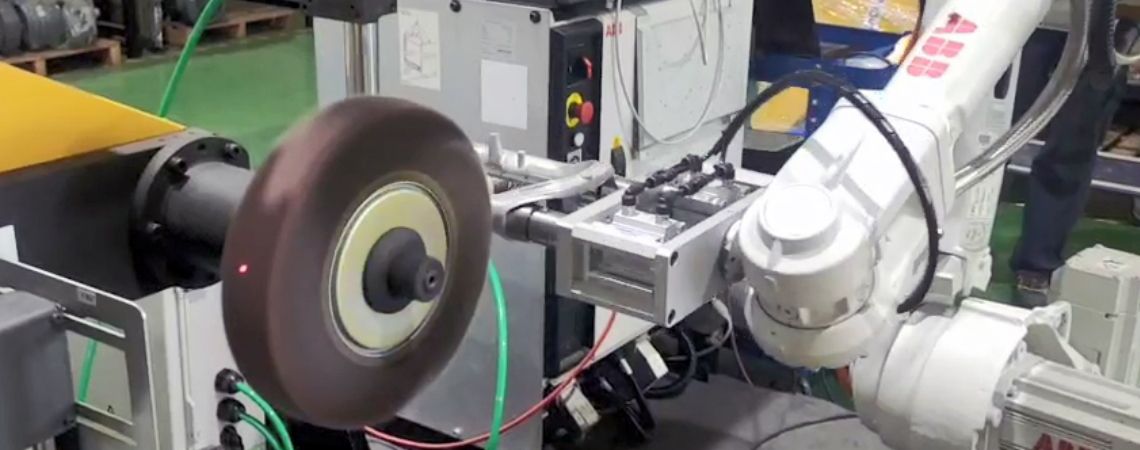
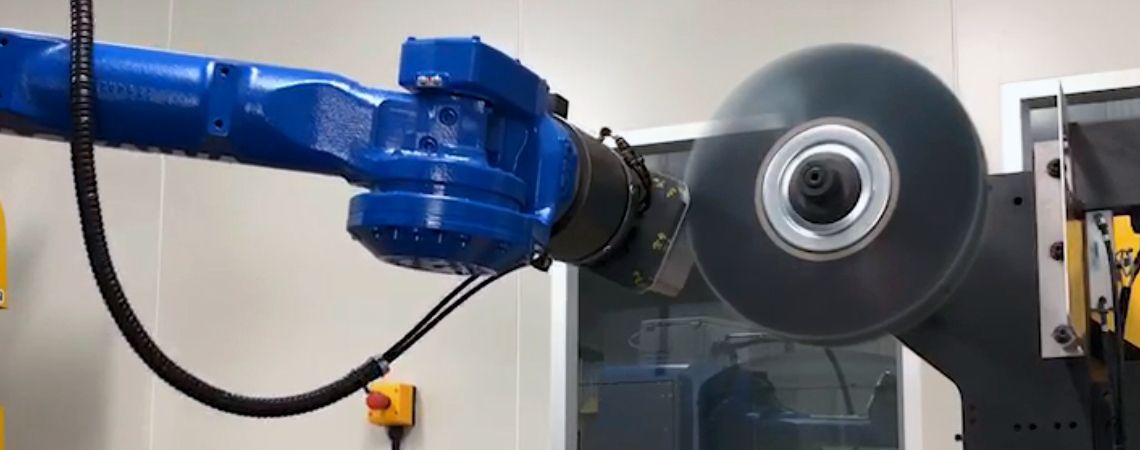
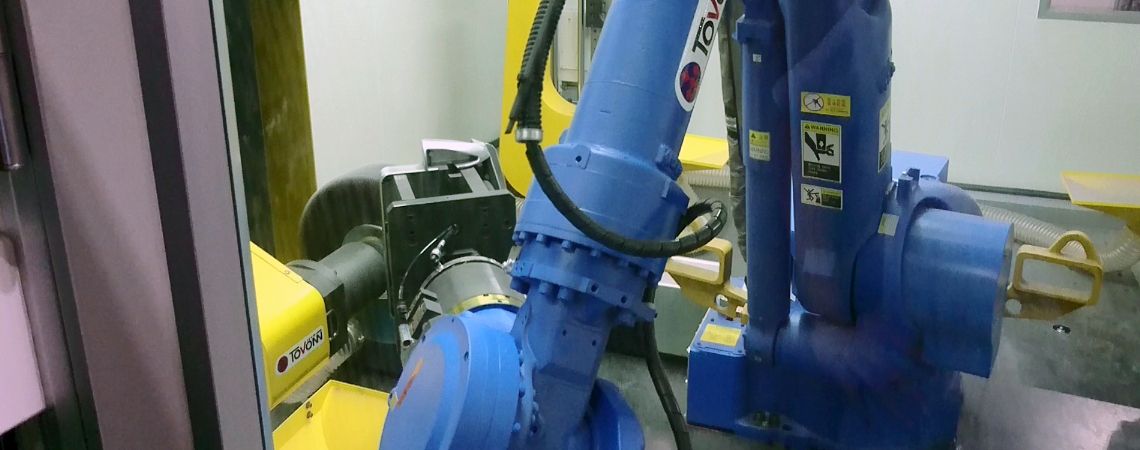
Intelligent Flap Wheel Machine, Dual-Axis Flap Wheel Machine
Flap Disc Machine, Wire Brush Machine, Sanding Machine, Polishing Machine
TOVONN Technology Corporation's smart flap wheel machine, designed to work seamlessly with grinding and polishing robotic arms, intelligent sanding machines, and floating deburring pneumatic tools, offers a modular peripheral grinding equipment solution, forming an all-in-one automated grinding unit. Leveraging the high repeatability precision of robotic arms, it effectively enhances product quality and efficiency.
The central control system of the grinding and polishing robotic arm can detect the wear condition of the flap wheel machine's abrasive materials, adjust grinding conditions and positions accordingly, maintaining a stable grinding effect.
The intelligent flap wheel machine features two grinding zones - upper and lower - accommodating two abrasive wheels with a diameter of up to 500mm. Examples of compatible grinding consumables include flap wheels, flap brushes, winged wheels, convolute wheels, non-woven wheels, and more. This machine is commonly used for grinding components with intricate curved surfaces.
Ideal for grinding and polishing components in aluminum alloy die casting, magnesium alloy die casting, zinc alloy die casting, iron casting, and copper alloy casting.
Features
1. Machine Dimensions: L x W x H (Approx.): 1200 x 600 x 1550mm
2. Servo Slide Travel: 200mm
3. Servo Slide Motor: Delta 400W Servo Motor
4. Explosion-proof Motor Specifications: 5HP, Three-phase 220V / 380V, 50 / 60Hz
5. Yaskawa Inverter Specifications: 3.7KW (5HP), Three-phase 380V x 1
6. Flap Wheel Machine Consumables Specifications: Inner hole 25mm, Maximum outer diameter not exceeding 400mm in diameter
7. Electrical Control Solenoid Valve Specifications: SMC-3120
8. Machine Appearance Colors: Body (White), Cover (Yellow), Other Extension Brackets (Black)
9. Automatic Compensation of Position and Speed when Grinding Material Wears.
10. Customizable Grinding Speed and Compensation Speed.
Product Advantages
● Meets ESG Requirements:
➔ Goal 8: Promote sustained, inclusive, and sustainable economic growth, full and productive employment, and decent work for all.
➔ 8.2 Through diversification, technological upgrades, and innovation, increase the capacity of the economy, focusing on high value-added and labor-intensive industries.
➔ 8.8 Protect the rights of workers, promote a safe working environment, including for migrant workers, especially women, and those engaged in hazardous work.
● Save Labor Costs: Combine overflow well trimming machines, punch presses, and dies to automate the production process of die casting, reduce the number of material handling times, and decrease manual processing time, lowering labor demand.
● Personnel Safety Protection: Previous manual operations required workers to insert their arms deep into the hydraulic punch press to retrieve or place castings, resulting in frequent unfortunate workplace incidents such as arm and finger injuries. This significantly contributes to protecting workers' health, as employee health is the company's greatest asset.
Robotic arm automation system integration.
Looking for Flexible Grinding Solutions That Integrate Seamlessly With Existing Robotic Systems?
TOVONN's modular flap wheel machine is designed for maximum integration flexibility, working seamlessly with Yaskawa, FANUC, and ABB robotic arms. The system features standardized communication protocols, compact footprint (1200 x 600 x 1550mm), and customizable grinding parameters that adapt to your specific application requirements. System integrators appreciate our comprehensive technical documentation and integration support, making this dual-axis grinding system one of the easiest automation components to incorporate into new or existing production lines. Contact us for integration specifications tailored to your project needs.
What sets this system apart is its intelligent compensation capability, which automatically detects abrasive material wear and adjusts grinding positions and speeds accordingly. The 400W Delta servo motor provides precise control over the 200mm slide travel, while the 5HP explosion-proof motor delivers powerful performance for demanding applications. The modular design allows integration with various peripheral grinding equipment, creating a comprehensive automated solution that enhances product quality, improves workplace safety, and significantly reduces labor costs—aligning perfectly with sustainable economic growth goals while protecting worker health and safety.