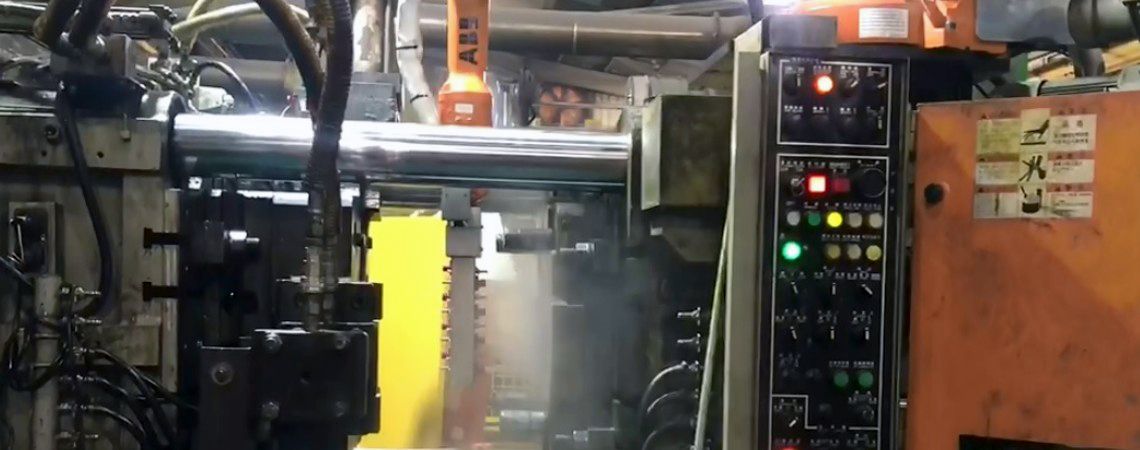
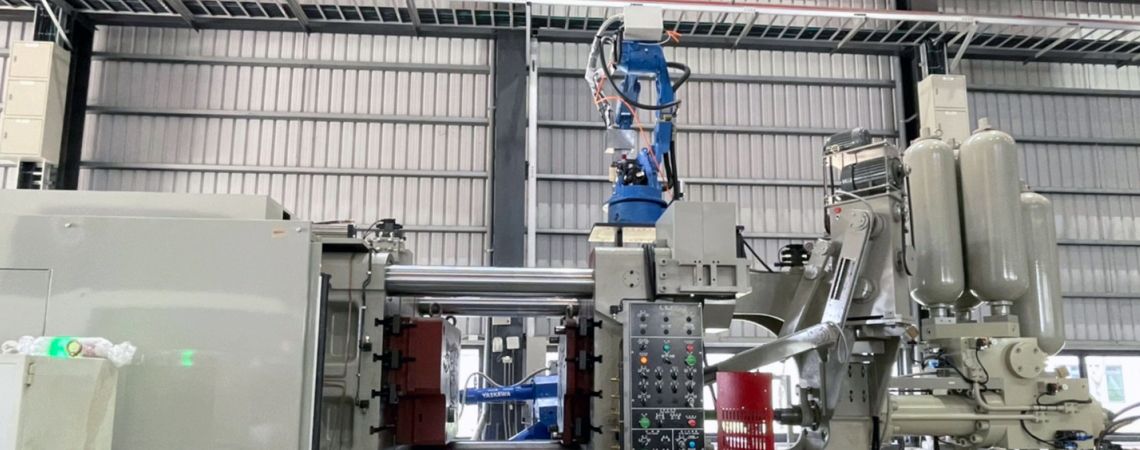
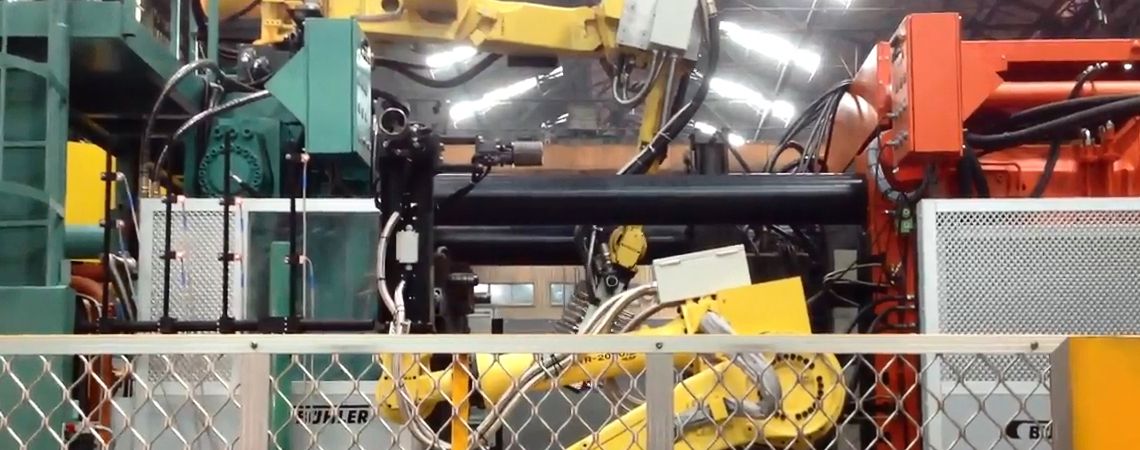
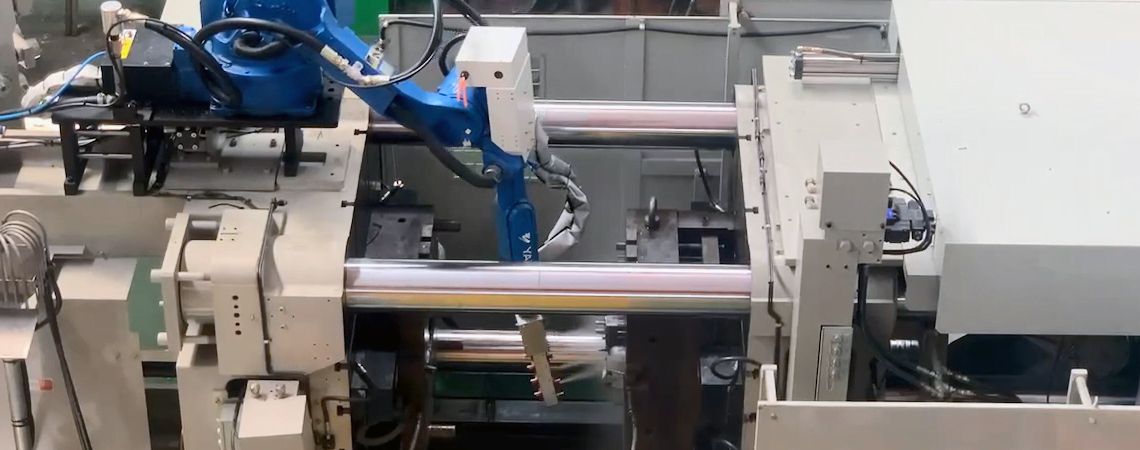
Die Casting Spray Automation System Integration
Die Casting Spray Automation, Die Casting Spray Robotic Automation System Integration
Enhance Efficiency with Advanced Die Casting Spray Automation
Transform your die-casting operations with our Die Casting Spray Automation System Integration, leveraging the unparalleled versatility of a six-axis robot arm. This cutting-edge system is designed to replace traditional spray mechanisms, providing superior spray effects that optimize the use of release agents and significantly improve economic benefits.
Key advantages of our system include:
- Precision Application: The six-axis robot arm delivers precise and consistent spray patterns, reducing material waste and ensuring uniform coverage.
- Cost Efficiency: By optimizing the use of release agents, our system cuts down on excess costs and minimizes environmental impact.
- Enhanced Productivity: With faster and more reliable spraying processes, our system boosts overall production throughput, maintaining high-quality standards without the need for frequent downtime.
- Operational Safety: Reduces human exposure to potentially hazardous materials and conditions, enhancing workplace safety.
This automation solution is ideal for businesses looking to increase efficiency, reduce costs, and improve the sustainability of their die-casting operations. The integration of robotic technology in spray processes not only secures product quality but also aligns with modern manufacturing practices that prioritize precision and resource conservation.
Die-casting extraction system, suitable for die-casting processes including:
- Die-casting extraction for cold chamber machines (aluminum alloy die-casting, magnesium alloy die-casting).
- Die-casting extraction for hot chamber machines (magnesium alloy die-casting, zinc alloy die-casting).
TOVONN Technology can collaborate with robotic arm manufacturers, including:
- YASKAWA (YASKAWA Robotics)
- FANUC (FANUC Corporation)
- ABB (ABB Robotics)
The die casting machine brands that Tovonn Technology has collaborated with include:
- TOYO (Toyo Die Casting Machine)
- TOSHIBA (Toshiba Machine)
- SHIBAURA (Shibaura Machine)
- TBC (Shangfu Die Casting Machine)
- HISHINUMA (Hishinuma Machinery)
- BUHLER (Buhler Group)
- UBE (UBE Machinery)
- FRECH (FRECH)
- Prince
- Italpresse
- L.K. Technology
- Producer Co., Ltd
- ZITAI PRECISION MACHINERY CO., LTD
Contact us today to learn how our Die Casting Spray Robotic Automation System can revolutionize your production line and yield substantial economic returns.
Robotic arm automation system integration.
How Does TOVONN Ensure Seamless Integration with Your Existing Die Casting Equipment?
With experience integrating with over 13 major die casting machine brands including TOYO, TOSHIBA, BUHLER, and UBE, TOVONN's engineering team specializes in creating custom interfaces that ensure perfect communication between robotic spray systems and your existing equipment. Our comprehensive compatibility with YASKAWA, FANUC, and ABB robotic platforms means we can design the optimal solution regardless of your current setup or future expansion plans. Schedule a technical consultation to discuss your specific integration requirements.
With over 40 years of casting industry expertise, TOVONN has developed spray automation systems that address the core challenges facing modern die casting operations. Our robotic spray solutions not only enhance operational efficiency through precise application patterns but also improve workplace safety by reducing human exposure to potentially hazardous materials. The system's advanced programming capabilities allow for customized spray patterns tailored to specific die geometries, ensuring optimal coverage while minimizing excess release agent usage. This translates to substantial cost savings, improved part quality, reduced cycle times, and a more environmentally sustainable production process for die casting manufacturers seeking competitive advantages in today's demanding market.