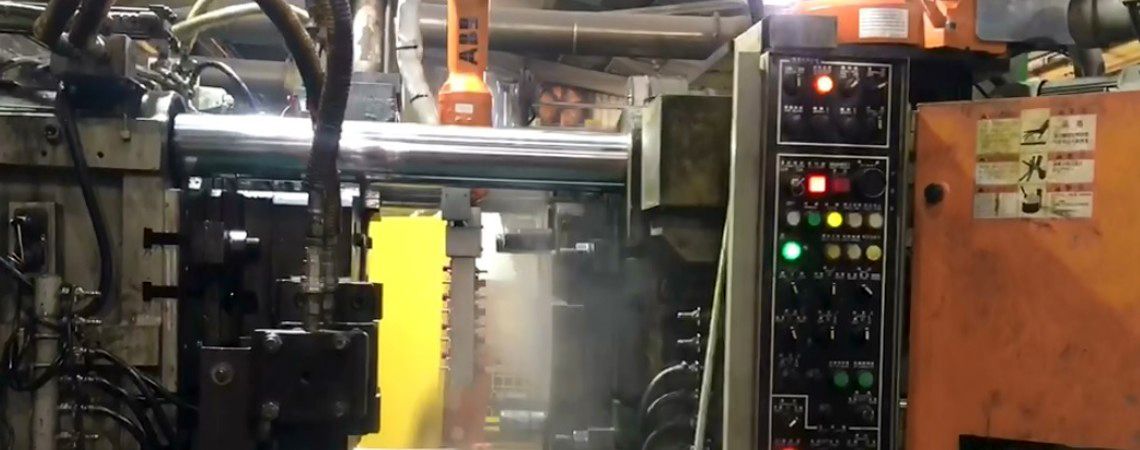
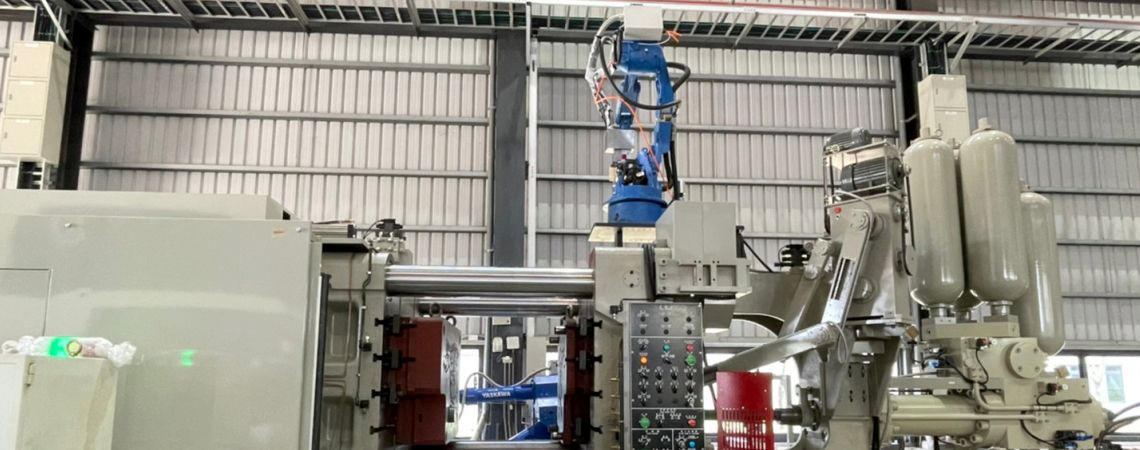
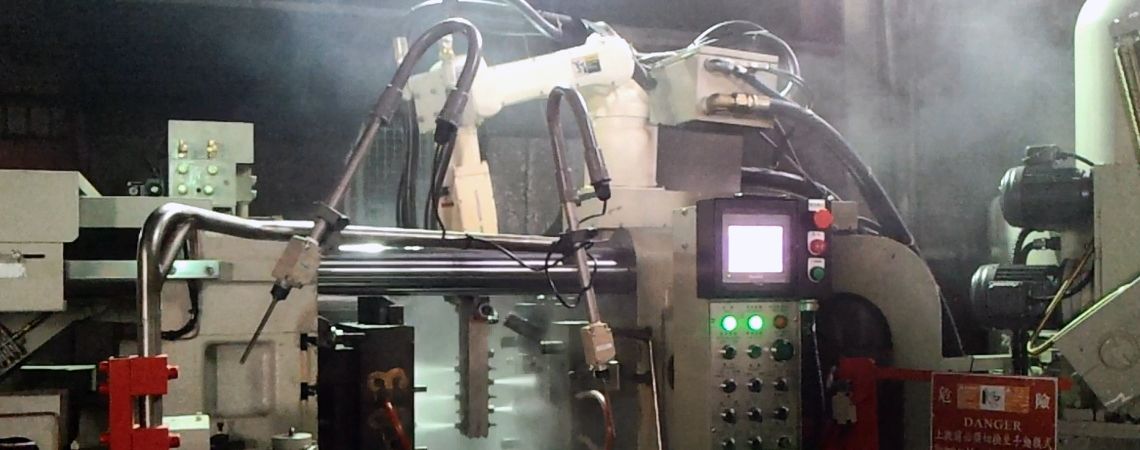
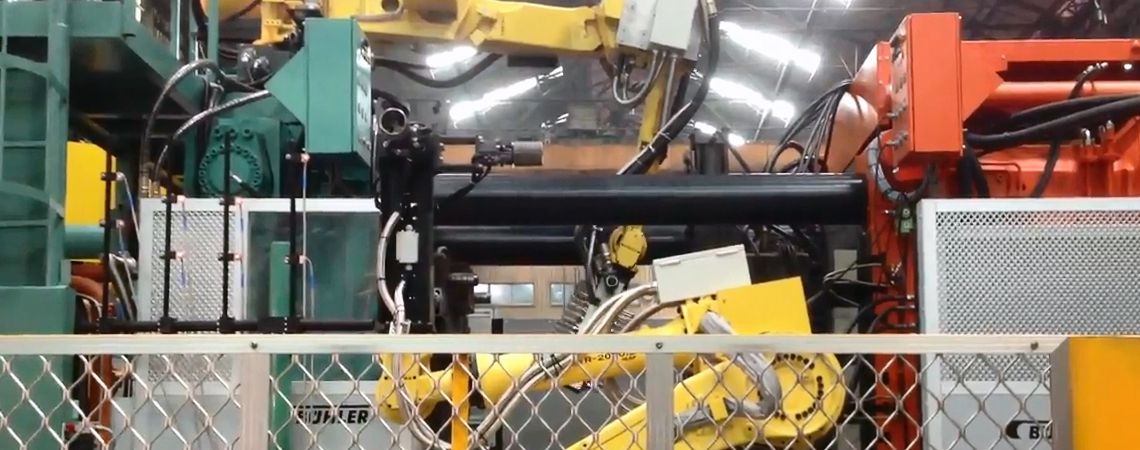
Spray Robotic Arm
Die Casting Release Agent Spray, Spraying Robotic Arm, Spraying Robot, Die Casting Spray Industrial Robot, Die Casting Mold Release Agent Spraying
The Spray Robotic Arm, developed by Tovonn Technology Corporation, provides professional solutions for spraying die-casting release agents, misting systems, and robotic spraying arms. It addresses a range of challenges that die-casting engineers may encounter.
The spraying system from Tovonn Technology incorporates intelligent flow sensing technology, allowing precise application of release agent to the hot spots of cold-chamber die-casting molds. This precision spraying helps effectively reduce mold temperatures, ensuring the quality of casting production.
Ideal for release agent spraying operations in cold-chamber die-casting machines.
Suited for use in the production of aluminum alloy and magnesium alloy die-castings.
Die Casting Engineers May Encountered the Following Challenges:
- Local areas of the mold have excessively high temperatures, and traditional spray systems cannot address specific mold hotspots, leading to challenges in localized cooling.
- Traditional spray systems leave blind spots during mold spraying, resulting in incomplete coverage and the potential for casting defects such as burn-on, reducing product yield.
- Deep mold sections make it difficult for traditional copper nozzle systems to effectively and uniformly spray release agents. Additional manual assistance is required to supplement spraying near the die-casting machine.
- Excessive usage of release agents by traditional spray systems results in high wastewater treatment costs.
- Lack of clarity on the varying amounts of release agents required for different castings.
- Difficulty in finding the appropriate spray nozzle for specific castings amid a cluttered and dirty setup.
- Tedious adjustments of copper pipes' angles and potential face exposure to release agents during setup with traditional spray systems.
If you are facing these challenges, please contact Tovonn Technology. We can discuss and plan how to automate the release agent spraying process in die-casting, ushering in the era of automation.
Spraying Process Upgrade: Tovonn Technology provides integrated solutions for robotic spraying.
Tovonn Technology provides comprehensive robotic spraying integration services, collaborating with robotic arm manufacturers such as YASKAWA, ABB, and FANUC. Our service range includes supplying robotic arms, release agent spraying tools and control systems, as well as debugging and programming tailored to specific castings.
By integrating release agent flow detection, we monitor the spraying volume of each production cycle. If deviations from the set standard are too significant, it indicates issues with the release agent pipeline or nozzles. Immediate notifications or alerts are sent to relevant personnel for inspection, reducing the rate of defective castings.
During the integration planning phase, we utilize 3D simulation software to define the workspace and installation space, laying the foundation for subsequent on-site programming. This approach minimizes trial and error time on-site, ensuring an efficient integration process. Tovonn Technology has the capability to integrate spraying technology with robotic arms and die-casting machines. We have connected to various die-casting machines, including TOYO, TOSHIBA, TBC, HISHINUMA, BUHLER, UBE, FRECH, Prince, Italpresse, LK Machinery, HSIN LIEN SHENG Machinery, ALTEK, and more.
Contact us now to understand how our robotic arm integration solutions can enhance your spraying process and meet your automation needs.
Features
- For die-casting machines below 250T: Straight 6-nozzle spray mechanism, with 3 each on the fixed and movable sides (standard spray mechanism).
- For 350T ~ 650T ~ 800T die-casting machines: Straight 8-nozzle spray mechanism, with 4 each on the fixed and movable sides (standard spray mechanism).
- For die-casting machines above 800T: Recommended to use horizontal spray mechanism with 10 - 12 nozzles (customized spray mechanism).
- Customized spray mechanisms: Feel free to contact us to discuss types and quantities.
- Each nozzle can be independently controlled for opening and closing, or several nozzles can be grouped for control.
- Blow functions for the fixed and movable sides can be controlled separately.
- Quick response valve opening and closing control at the nozzle front.
- Nozzles controlled using compact standard solenoid valves, saving space.
- External mixing of air and release agent for excellent atomization.
- Compact spray mechanism with agile movement, minimizing dead angles in spraying.
- Extended pipelines can be installed at the front of the nozzle for deep spraying into the mold.
- Aperture of release agent passages is greater than 1.8mm, preventing blockages by impurities.
- Optimal spraying of the right amount of release agent at suitable positions in the mold, reducing consumption and minimizing mold temperature drop.
- Concentrated spraying on mold hotspots to avoid sticking and burning, ensuring balanced mold temperature.
- Robot program selection for different mold spraying angles and positions, eliminating the need for copper pipe seat storage and management, reducing mold changeover time.
-
Standard spray mechanism: Straight 6 nozzles, for 250T die casting machine
-
Standard spray mechanism: Straight 8 nozzles, for 350T die casting machine
-
Customized spray mechanism: Horizontal 8 + 2 nozzles, for 800T die-casting machine
Product Advantages
● ESG Compliance: Meets Environmental, Social, and Governance requirements by conserving air and release agent consumption, reducing harmful substances in the air, saving energy, and lowering wastewater treatment costs.
● Labor Cost Savings: Robotic arms can operate around the clock, saving the equivalent of two shifts of manual labor.
● Reduced Production Costs: Compared to manual spraying, automated control of spraying precisely manages the amount of release agent, reducing costs associated with release agent consumption and wastewater treatment.
● Personnel Safety Protection: Previous manual operations required workers to wear masks and goggles to protect against release agents and smoke, but the effectiveness was limited, leading to long-term impacts on lung function. Additionally, manual spraying involves placing arms within the working range of die-casting machines, resulting in unfortunate workplace accidents such as crushed arms or fingers. Automation significantly contributes to worker health protection, recognizing that employee well-being is a company's paramount interest.
Function Comparison Table with Traditional Sprayers
Traditional Sprayer | Tovonn Spray Robotic Arm | |
---|---|---|
Nozzle Control | All nozzles: spray together and turn off together. | The nozzle can be opened and closed independently. |
Spray Effect | After mixing inside the spray seat, it is spit out through the copper pipe, and the atomization effect is poor. | External mixing at the front end of the nozzle, good atomization effect. |
Spray Dead Spot | Many The depth of the mold is too deep and the spray position cannot be sprayed. The position of the spray is too high or too low to spray. |
Few Paired with a six-axis robot, high flexibility. |
Release Agent Dosage | Many No difference spray. |
Few Spray only where needed. |
Manage | Different molds correspond to different storage, management, and placement spaces for copper tube holders. | Program storage Access via flash drive, can correspond to unlimited sets of molds. |
Cycle Time Of Spray | Short. | Close to traditional spray, slightly more. |
Spray Adjustment | Bending copper pipes is suitable for low-level technicians. | Program and software control Requires robot operation training. |
Robotic arm automation system integration.
How Can Spray Robotic Arms Address Both Your ESG Goals and Worker Safety Concerns?
TOVONN's Spray Robotic Arm solutions deliver measurable ESG benefits through reduced air and release agent consumption while significantly enhancing worker safety. By automating the spraying process, we eliminate worker exposure to harmful substances and dangerous machine zones that have historically led to serious workplace injuries. Our systems operate 24/7, replacing two shifts of manual labor while providing precise documentation of material usage for environmental compliance reporting. Schedule a demonstration to see how our technology can transform your operation's sustainability profile and safety standards.
Developed with over 40 years of casting industry expertise, TOVONN's spray robotic integration services combine the precision of six-axis industrial robots from YASKAWA, ABB, and FANUC with our proprietary spraying technology. This comprehensive solution addresses key challenges facing die casting engineers, including hotspot management, blind spot elimination, deep mold section coverage, and excessive release agent consumption. By implementing our robotic spray systems, manufacturers achieve significant reductions in production costs, enhanced worker safety, improved ESG compliance, and consistent product quality—all while minimizing manual intervention and maximizing operational efficiency.