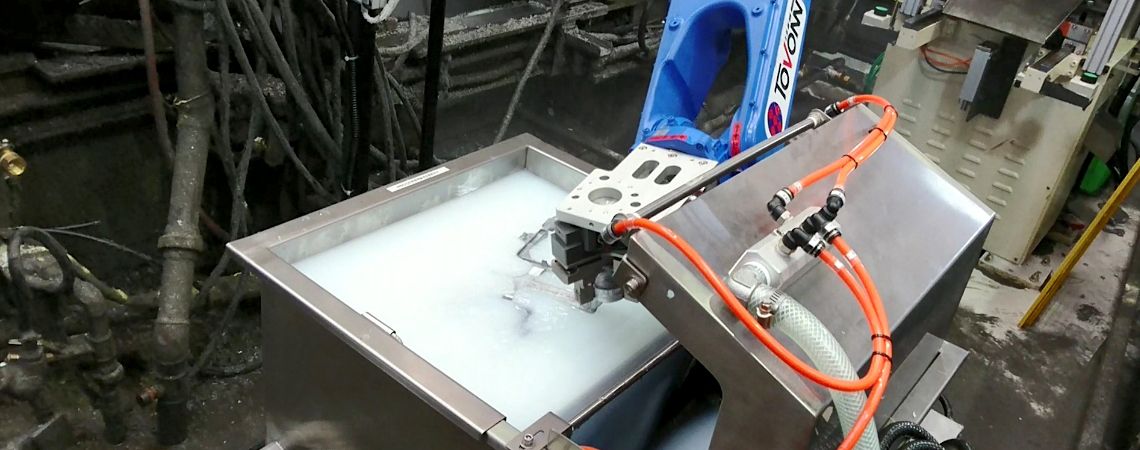
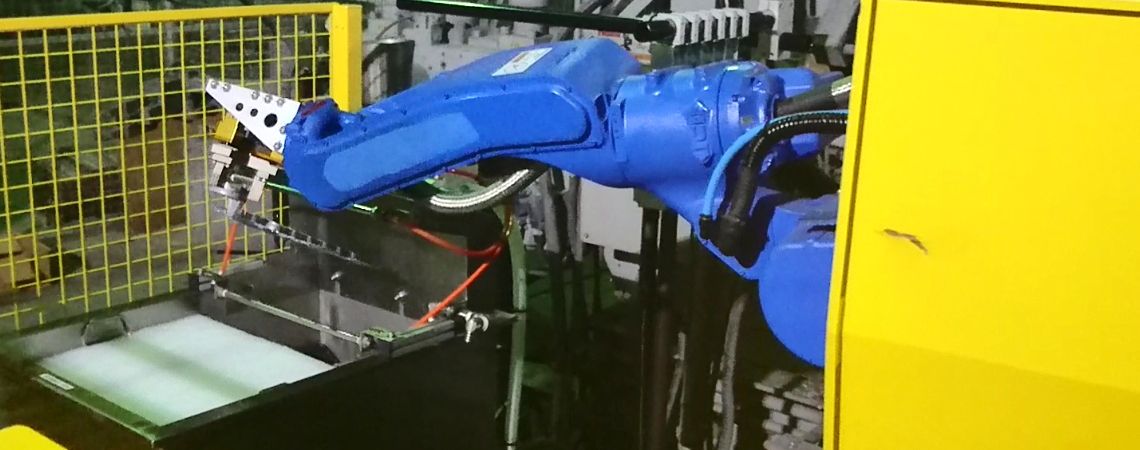
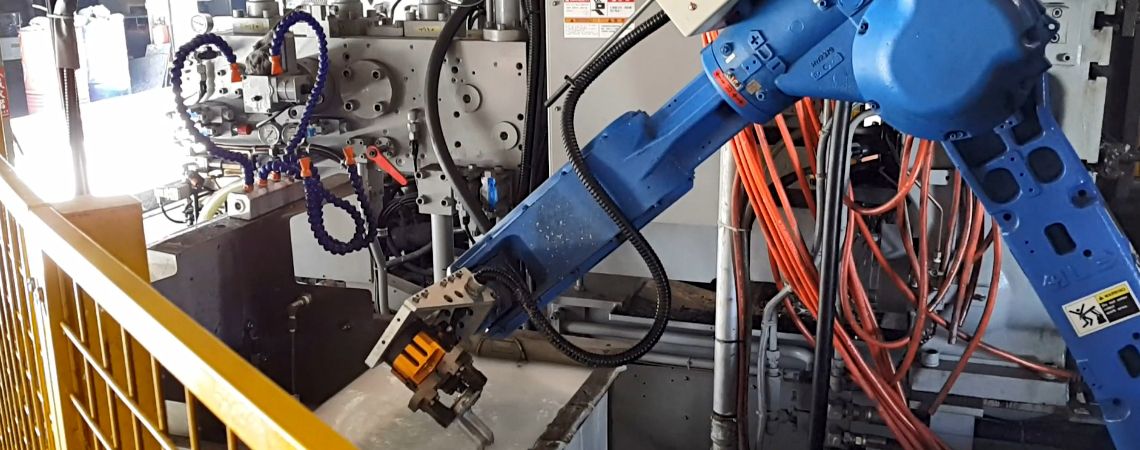
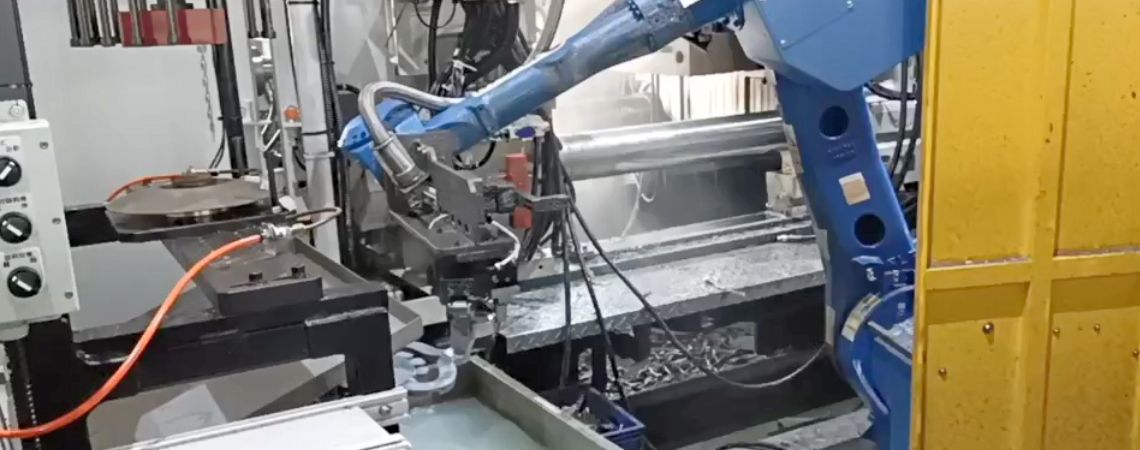
Casting Cooling Water Tank
Temperature-Controlled Cooling Water Tank, Temperature Controlled Tank
Tovonn Technology designs a casting cooling water tank that can be integrated with a multi-functional hydraulic shearing and punching press, as well as a die-casting extraction robotic arm for automated production. After the robotic arm extracts the casting from the die-casting machine, the casting remains at a high temperature and cannot be immediately sheared on the hydraulic punching press. Therefore, it is necessary to lower the temperature through the cooling water tank.
The casting cooling water tank is equipped with cooling fins inside and can be connected to the die-casting machine's cooling water system to reduce the temperature of the water in the tank. There is an air knife on top of the tank to quickly blow off any remaining water on the casting's surface. For castings that are not suitable for immersion in water, it is recommended to use an air-cooled rack to reduce the casting temperature.
The cooling water tank can also be paired with a trimming machine, with the lower half being the water tank and the upper half being the trimming machine, saving installation space and movement time. The trimming machine can remove overflow wells, burrs, and other elements, reducing waste generation on the hydraulic punching press.
This system is suitable for castings from both cold-chamber and hot-chamber die-casting machines, and it is appropriate for the production of aluminum alloy and zinc alloy die-castings. However, for zinc alloy die-casting and castings with a production cycle time of less than 20 seconds, a careful discussion and evaluation are necessary to determine suitability.
Features
1. Machine Dimensions L x W x H (Approx.): 700 x 1000 x 1300mm
2. Water Tank Capacity: 250L
3. Pump Motor Brand: KIKAWA 0.37kw, 1φ 220V
4. Water Tank Cooling Method: Water-cooled (3/4")
5. Water Tank Material: SUS304
6. Air Knife.
Product Advantages
● Meets ESG Requirements:
➔ Goal 8: Promote sustained, inclusive, and sustainable economic growth, full and productive employment, and decent work for all.
➔ 8.2 Enhance economic productivity through diversification, technological upgrading, and innovation, focusing on high-value and labor-intensive industries.
➔ 8.8 Protect labor rights and promote a safe working environment, including for migrant workers, especially women, and those engaged in hazardous work.
● Cost Savings in Labor: Integrating the overflow well trimming machine, punching press, and die enables the automation of the die-casting extraction process, reducing material handling frequency and manual processing time, thus lowering labor requirements.
● Personnel Safety Protection: In manual operations, workers previously needed to extend their arms deep into the hydraulic punching press to extract or place castings, exposing their limbs within the working range of the hydraulic punching press. This often resulted in unfortunate workplace incidents such as crushed or injured limbs and amputations. This significantly contributes to the health protection of workers, as employee well-being is a company's foremost interest.
Robotic arm automation system integration.
How can automated cooling systems impact your die casting production efficiency?
Our temperature-controlled cooling water tank reduces casting cycle times by up to 30% while eliminating manual handling risks. By integrating Yaskawa robotic arms with our cooling system, aluminum die casting manufacturers can maintain consistent product quality, reduce labor costs, and increase throughput. The system's precise temperature control ensures optimal cooling rates for various casting geometries, preventing warping and dimensional issues common in manual processes.
What sets our system apart is its multi-functional capabilities, combining cooling with optional trimming functionality to save valuable production space and reduce cycle times. The system's 250L capacity and KIKAWA 0.37kw pump motor deliver consistent performance for both aluminum and zinc alloy applications. By automating the cooling process, TOVONN's solution significantly enhances workplace safety by eliminating manual handling of hot castings, directly supporting ESG goals 8.2 and 8.8 through technological upgrading and worker protection. This integrated approach reduces labor requirements while preventing common workplace injuries associated with manual die casting operations.