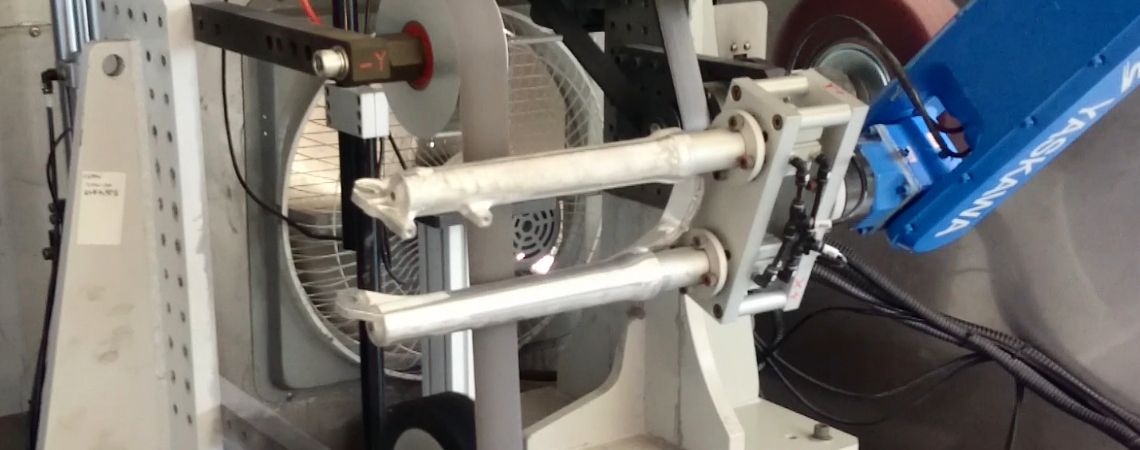
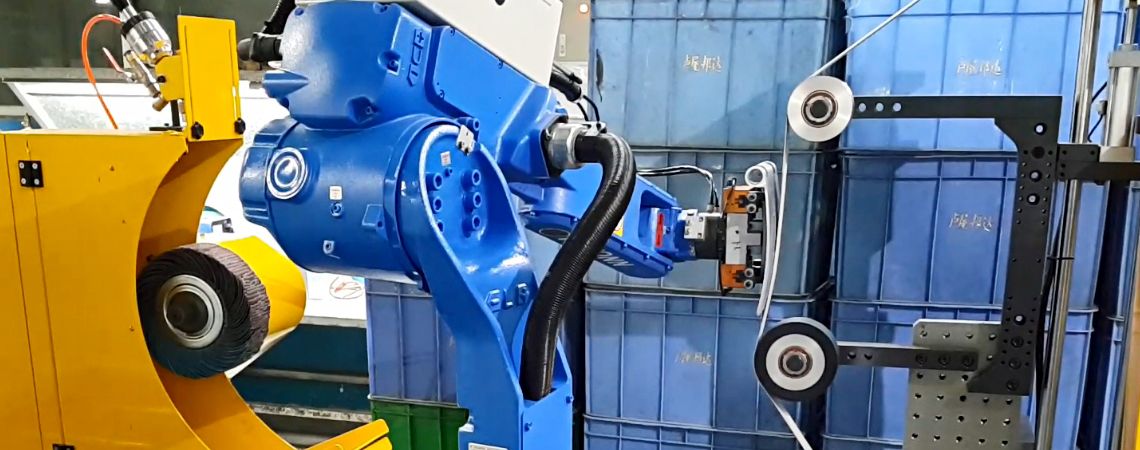
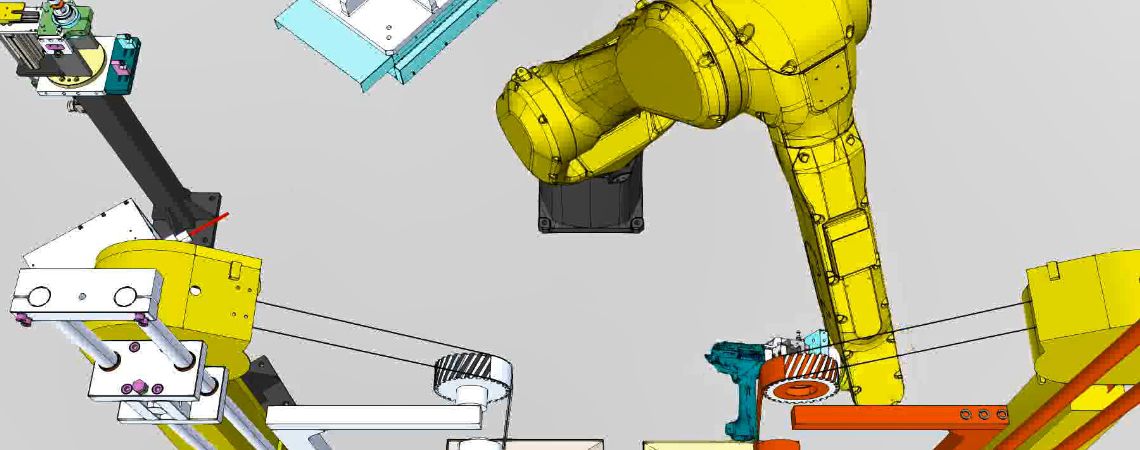
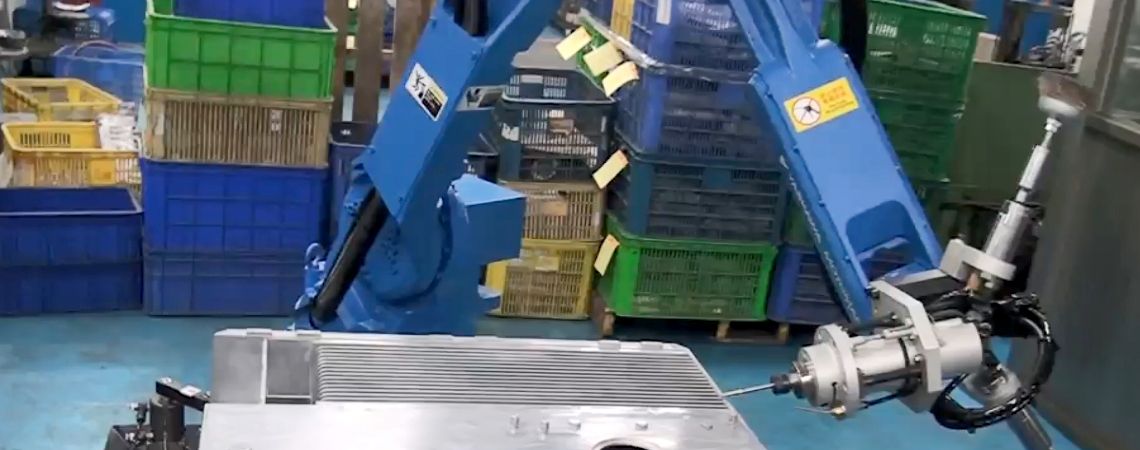
Grinding and Polishing Robotic Arm
Polishing Robot, Buffing Robot, Polishing and Buffing Automation System
The Grinding and Polishing Robotic Arm, provided by Tovonn Technology, offers professional solutions for deburring, grinding, and polishing in die casting systems. It addresses a range of challenges that die casting engineers face.
Tovonn Technology's grinding and polishing system integrates intelligent belt sanding machines, intelligent Chiba wheel machines, intelligent cloth wheel machines, and pneumatic tools for floating deburring. It offers modular peripheral grinding equipment solutions, forming a comprehensive grinding automation unit.
Taking advantage of the high repeatability precision of robotic arms effectively enhances production quality and efficiency. This solution reduces the risks of environmental hazards, ensures labor safety, and addresses challenges related to labor shortages and difficult management.
Particularly suitable for the deburring and grinding of die-castings with diverse positions, larger dimensions, and heavier weights. Applicable to the grinding and polishing of castings in aluminum alloy die casting, magnesium alloy die casting, zinc alloy die casting, cast iron casting, and copper alloy casting.
Challenges in Casting Grinding & Polishing for Engineers
- Difficulty in finding workers to remove burrs from castings.
- Challenges in finding skilled grinding workers, with a long learning curve for new hires, and potential difficulties with employee training.
- Desire to outsource the grinding process but unable to find suitable vendors.
- Inconsistent quality of finished castings after grinding, with variations in depth, sometimes too deep, sometimes too shallow, and occasional oversights.
- Heavy workpieces that are difficult to flip, risking injuries to workers' wrists.
- High dust concentration in the air, a dirty environment, leading to respiratory issues for workers such as silicosis, causing occupational hazards and disputes between labor and management.
If you are facing these challenges, please contact Tovonn Technology. Let's discuss and plan how to bring the grinding and polishing of castings into the world of automation.
Grinding and Polishing Process Upgrade: Tovonn Technology offers robotic arm grinding and polishing integrated solutions.
Tovonn Technology offers comprehensive robotic arm grinding, polishing, and deburring integration services, collaborating with robotic arm manufacturers such as YASKAWA, ABB, and FANUC. Our services include providing robotic arms, grinding grippers and fixtures for castings, control systems, as well as debugging and programming grinding processes tailored to specific castings. Educational training provided covers basic robotic arm operations, experience sharing in writing grinding and polishing programs, selecting grinding consumables, and imparting tips on robotic arm operation, assisting customers in quickly becoming familiar with the related equipment.
Combined with Tovonn's independently developed grinding system monitoring and settings, as the number of castings being ground increases, the system gradually speeds up motor rotation or adjusts the position of the grinding machine to accommodate the wear and tear of grinding consumables such as sandpaper, Chiba wheels, and cloth wheels.
During the integration planning phase, we use 3D simulation software to define the workspace, equipment, and installation space, laying the foundation for subsequent on-site programming. This reduces trial-and-error time on-site, ensuring an efficient integration process.
Please contact us now to learn how our robotic arm system integration solutions can enhance your grinding process and meet your automation needs.
Features
- Speed control for the belt sander, allowing customers to set parameters based on different castings.
- The Chiba wheel machine adopts a dual-axis design, enabling customers to place different grinding consumables according to their actual needs.
- The Chiba wheel machine is equipped with a movable sliding table that automatically corrects the equipment position when consumables wear out.
- Deburring tools utilize floating milling cutters and floating file machines, providing flexible contact with the burrs on castings, absorbing deviations and tolerances, maintaining a consistent contact force.
- Robotic arms can be equipped with pneumatic infinite rotation mechanisms to reduce issues such as hose entanglement and interference at the front end of the sixth axis. It is compatible with robotic arms from brands such as YASKAWA, FANUC, ABB, etc. For YASKAWA GP25, a hollow structure in the sixth axis allows embedding the rotation mechanism, reducing the volume at the front end of the robotic arm.
- Can be paired with a 3D CCD system for automatic positioning and grabbing of castings for grinding, eliminating the need for fixture production costs and storage space.
- Utilizing offline programming software DELFOi for robotic arms, leveraging the surface features and topological structure of 3D CAD models, the multifunctional and parametric path creation tools enable the quick and easy creation of different toolpath patterns on surfaces.
Product Advantages
● Compliance with ESG Requirements: Achieving ESG goal 8.2 by enhancing the economic capacity through diversification, technological upgrades, and innovation, particularly focusing on industries with high added value and labor intensity. Simultaneously, meeting goal 8.8 by safeguarding workers' rights, promoting workplace safety, especially for migrant workers, women, and those engaged in hazardous work.
● Integration of Partitions and Dust Collection Devices: Through the use of partitions and dust collection devices, the majority of metal dust and cutting waste are effectively contained within designated areas, thereby reducing pollution to the overall factory environment. This also aids in protecting employees from prolonged exposure to high-dust environments, mitigating potential impacts on lung and respiratory health.
● Personnel Safety Protection: In contrast to manual operations where workers need to wear masks and goggles for dust and cutting protection with limited effectiveness, modernized operational methods significantly enhance protection, preventing prolonged exposure to environments that may affect lung functionality. Additionally, automation reduces the occurrence of hand injuries and cuts during manual grinding operations, effectively promoting the health and safety of employees.
● Ensuring Consistency in Product Grinding Quality: Automation contributes to ensuring consistent product grinding quality while reducing the need for manual grinding labor. This not only improves production efficiency but also helps minimize the impact of human errors on product quality.
Function Comparison Table with Traditional Manual Grinding
Traditional Manual Polishing | Tovonn Technology Grinding Robotic Arm | |
---|---|---|
Grinding Positions | Flexible with fewer blind spots. | Prone to blind spots or interference, leading to difficulties in grinding. |
Grinding Speed | Fast | Slow |
Grinding Quality | Experienced Workers: Excellent Newly hired workers: Unstable Prone to overlooking and leaving ungrinded conditions. |
Maintains Consistency Fixed program paths, ensuring no omissions in grinding positions. |
Grinding Time | Lightweight Products: Short Heavyweight products: Approximate |
Lightweight Products: Long Heavyweight products: Approximate, slightly more |
Skill Acquisition Time | Long training time | Long learning time for program coding. |
Robotic arm automation system integration.
What makes TOVONN's approach to complex alloy part finishing more efficient than competitors?
TOVONN's distinctive advantage lies in our comprehensive integration methodology. We utilize advanced DELFOi offline programming software that leverages 3D CAD models to create optimized toolpaths specifically designed for complex aluminum and magnesium alloy geometries. This simulation-first approach dramatically reduces on-site programming time and trial-and-error adjustments. Combined with our floating deburring tools that automatically adjust to part variations, our systems achieve consistent results even with the challenging surface complexities typical of lightweight alloy castings.
Engineered with both productivity and ESG compliance in mind, our robotic grinding systems incorporate sophisticated features including speed-controlled belt sanders, dual-axis Chiba wheel machines with automatic position correction, pneumatic infinite rotation mechanisms, and compatibility with 3D CCD positioning systems. TOVONN's solutions dramatically reduce workplace hazards by containing metal dust through integrated partitioning and dust collection, while simultaneously ensuring consistent product quality that manual processes cannot achieve. Each system includes comprehensive support with 3D simulation planning, programming assistance, and educational training to ensure rapid implementation and maximum return on investment.