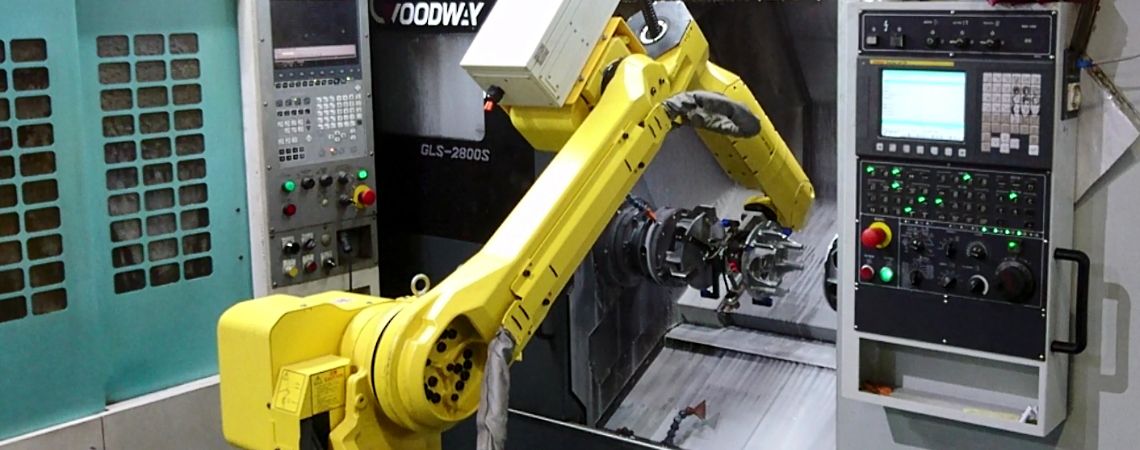

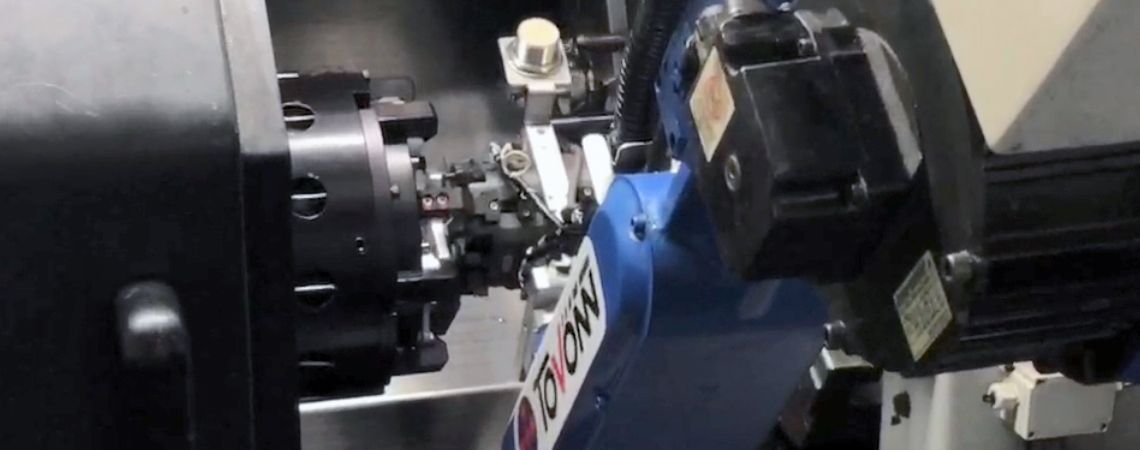
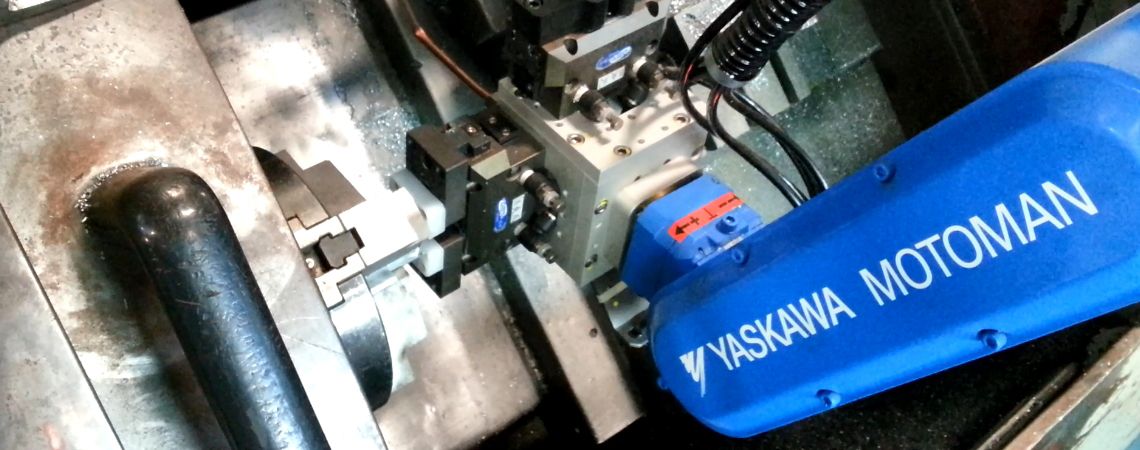
Lathe Machine Tending System Integration
Lathe Loading and Unloading, Lathe Loading and Unloading System, Lathe Loading and Unloading Robot Arm, Lathe Pick and Place Robot, Lathe Handling Robot Arm
TOVONN Technology provides professional lathe loading and unloading functions, loading and unloading systems and loading and unloading robotic arm solutions, solving a series of problems that engineers may encounter.
TOVONN Technology's loading and unloading system can be equipped with peripheral equipment, such as: workpiece turning mechanism, workpiece guiding mechanism, workpiece feature identification system, specific character identification system, cutting air blowing removal mechanism, workpiece cleaning equipment, laser engraving text and pattern equipment, Workpiece stacking function, product appearance inspection equipment, product size inspection equipment...etc., meet all the needs of the lathe processing process.
It is suitable for automated production of workpiece handling and workpiece pick-and-place of various lathe processing machines.
Suitable for lathe processing and production of aluminum alloy die castings, magnesium alloy die castings, zinc alloy die castings, copper alloy workpieces, and gravity casting workpieces.
Dear hard-working engineers, have you ever had the following problems:
- The boring and tedious loading and unloading work on lathes, but you often can't find suitable operators?
- The lathe machine takes a long time to process a workpiece. When the processing is completed, the operator does not replace the workpiece immediately, making the processing time longer?
- The lathe machine takes a very short time to process the workpiece. The operator needs to frequently change the workpiece. Is the workload too heavy?
- The workpiece must be placed on the chuck of the lathe at a specific angle, but operators often ignore it when placing it, resulting in abnormal processing and incorrect dimensions?
- The dimensions processed by the lathe were abnormal. When the inspection quality assurance personnel found out, many workpieces with abnormal quality had been produced?
If you have these pains, please contact TOVONN Technology, and the two parties will discuss and plan how to load and unload the workpieces of the lathe into the world of automation.
Lathe loading and unloading process upgrade: TOVONN Technology provides integrated loading and unloading solutions for robotic arms
TOVONN Technology provides comprehensive robotic arm removal integration services, and cooperates with robotic arm manufacturers including YASKAWA, ABB, and FANUC. Our service scope includes providing the setting and selection of robotic arms, action planning for loading and unloading, design of clamping jaws and control systems for loading and unloading, as well as debugging and programming for specific workpieces.
The lathe loading and unloading system can meet the customer's feeding needs and be matched with different feeding systems, such as: front and rear sliding table feeding systems, conveyor belt feeding systems, pallet feeding systems, warehouse feeding systems, and stack feeding systems. Material system, visual recognition feeding system...etc.
If there is a need to turn over the workpiece in the lathe processing program, it can be equipped with a workpiece turning mechanism to change the angle of the workpiece to meet the needs of different clamping positions of the lathe.
The lathe loading and unloading system can be used with multiple lathes and milling machines to meet diverse processing processes. TOVONN Technology will help customers calculate reasonable machine configuration options based on the processing time of various processes to maximize output.
When there are requirements for the placement angle between an asymmetric workpiece and the lathe chuck, a visual recognition system (CCD) can be used to identify workpiece features or specific text, so that the loading and unloading jaws can clamp the workpiece at the correct angle, and other factors can also be eliminated. The mixing of model workpieces causes quality abnormalities.
In the planning and integration stage, we will place lathes, robotic arms, and peripheral equipment on a 2D floor plan to discuss the loading and unloading action process and scope of activities. If necessary, we will use 3D simulation software to define the work area and installation space to prepare for the subsequent on-site Programming lays the foundation, reduces on-site exploration and trial and error time, and ensures an efficient integration process.
TOVONN Technology has the ability and experience to integrate loading and unloading technology with robotic arms, lathes, and processing equipment. Please contact us today to learn how our robotic arm integration solutions can improve your loading and unloading processes and meet your automation needs.
Features
- Workpiece clamping mechanism: According to the customer's workpiece characteristics, three-jaw parallel clamps, two-jaw parallel clamps, vacuum suction cups, electromagnets, etc. can be selected. In order to save moving time, there are usually multiple clamping mechanisms to clamp unprocessed and processed workpieces respectively.
- For specific installation quantities or detailed specifications, please contact Tongwang Technology for discussion.
- Corresponding to the chuck characteristics of the lathe processing machine, the workpiece clamping jaw mechanism is optional: an ejection mechanism to assist the clamping jaws in placing the workpiece into the lathe's chuck.
- In view of the differences in workpiece position and angle caused by large-scale feeding methods, or when the lathe processing process requires changing the workpiece clamping position, it can be equipped with: workpiece turning mechanism and workpiece guiding mechanism.
- When the workpiece has a special shape or specific text or symbols and needs to be placed on the lathe chuck at a specific angle, it can be used with: workpiece feature identification system, specific text identification system, and a simple visual identification system for identification.
- To avoid abnormal processing quality due to wear or breakage of lathe processing tools, it can be used with: product appearance inspection equipment and product size inspection equipment to achieve 100% quality inspection.
-
Workpiece Guide Fixture
-
Grippers for Lathe Loading and Unloading
-
Workpiece Feeding System
-
Workpiece Turning Mechanism
Product Advantages
● Comply with ESG Requirements:
➔ Goal 8: Promote sustained, inclusive and sustainable economic growth, full and productive employment and adequate work for all.
➔ 8.2 Increase the economy's production capacity through diversification, technological upgrading and innovation, including focusing on high value-added and labor-intensive industries.
➔ 8.8 Protect the rights and interests of workers and promote a safe working environment, including migrant workers, especially women and workers who perform hazardous work.
● Save Labor Costs: Utilize the flexibility of the robotic arm and peripheral equipment to automate the production process of lathe loading and unloading, reducing manpower requirements.
● Personnel Safety Protection: When workers are loading and unloading materials on the lathe, they have to put their arms deep into the lathe to take out and place the workpieces. This has certain safety concerns. Unfortunate accidents such as fingers being cut by the burrs of the workpieces or fingers being pinched by the chuck often occur. An incident. Automation of loading and unloading will greatly benefit the health protection of workers, and employee health is the company's biggest interest.
Function Comparison Table with Traditional Manual Loading and Unloading
Manual Loading And Unloading | Machine Tending Robot | |
---|---|---|
Pick and Place Flexibility | High Workpiece placement can be matched with almost any gripper and jig. |
Medium Requires cooperation between clamping jaw and jig. |
Pick and Place Stability | High However, repetitive and boring pick-and-place actions can tire personnel and lead to errors. |
High With the assistance of peripheral equipment, maintain a certain production rhythm. |
Pick-up and Drop-off Time | Quick Human hands are omnipotent. |
Slow Limited by the design and number of clamping jaws. |
Feature Check | Quick But it's easy to ignore it because of fatigue. |
Medium Stability check according to the programmed path. |
Robotic arm automation system integration.
How can robotic arm integration improve your lathe production efficiency while reducing labor costs?
TOVONN's lathe machine tending systems automate repetitive loading/unloading tasks with customized clamping mechanisms (three-jaw parallel, two-jaw parallel, vacuum suction cups, or electromagnets) that maintain consistent production rhythms even during long shifts. Our systems reduce labor requirements by up to 80% while increasing machine utilization by eliminating human-caused delays and errors, resulting in significantly higher throughput and consistent quality across all production runs.
With over 20 years of industry experience, TOVONN's lathe automation systems are engineered to optimize production efficiency while reducing operational costs. Our integration approach includes detailed 2D floor planning and 3D simulation to ensure optimal placement of equipment, minimizing installation time and maximizing workflow efficiency. Each system can be equipped with advanced features including workpiece feature identification, quality inspection equipment, and specialized handling mechanisms to accommodate your specific production requirements. By implementing our robotic arm integration solutions, manufacturers can achieve sustained production rhythms, enhanced worker safety, and consistent product quality while meeting ESG requirements for sustainable industrial development.